Rely on us to find the right industrial architectures for your new or transforming industrial systems — with a systemic approach that finds the right balance between business goals, technical feasibility, and long-term scalability.
Designing a new industrial system is a critical business decision. Our role is to help you derisking these strategic investments by providing an holistic analysis of your future industrial operations and finding viable, high level design options in time sensitive context, before you need to order costly equipment and launch complex analyses.
We combine model-based systems engineering, systemic modeling, data intelligence, and scenario-based simulation and collaborative techniques to:
- Evaluate and compare different design options under realistic operational conditions
- Quantify the business value and risks of each design choice
- Ensure performance, robustness and agility in the face of uncertainty
- Build alignment between business teams, technical experts, and project stakeholders
Our proven methodology enables faster decision-making, better cross-functional collaboration, and long-term operational success.
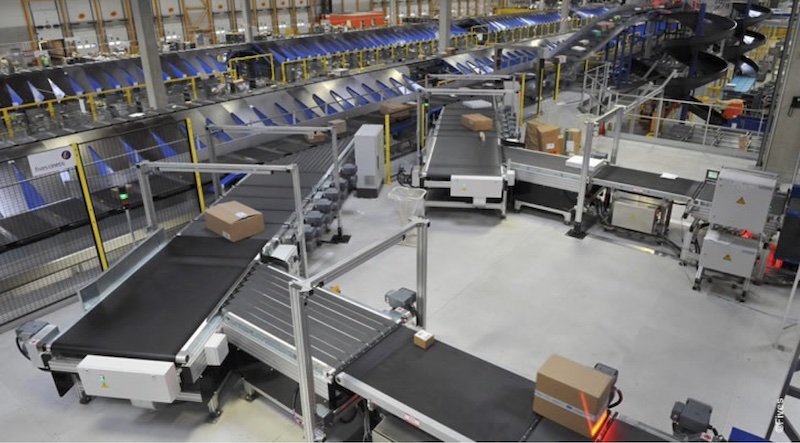
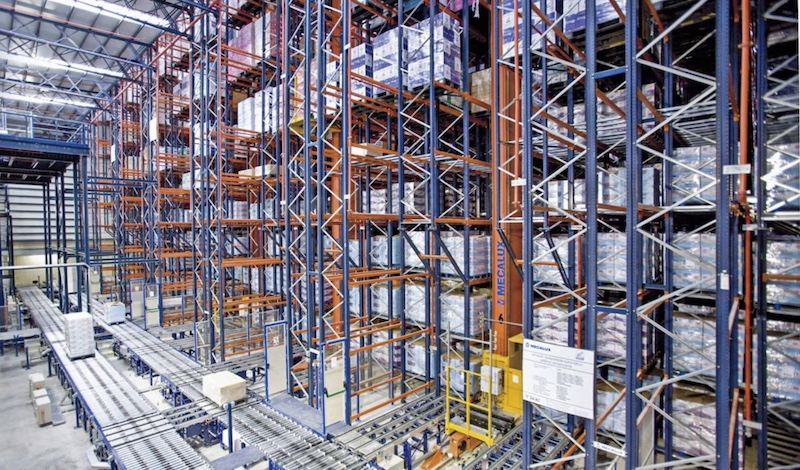

- Built a shared, transversal business vision of warehouse dynamics across all stakeholders (design, sales, and operations).
- Identified optimal warehouse designs aligned with customer business needs and operational constraints.
- Enhanced ability to manage seasonality, disruptions, and industrial resource variability.
- Improved confidence in investment decisions and customer engagement.
- Size fleets of machines, AGVs, and lifting equipment.
- Define buffer and storage areas.
- Identify bottlenecks and optimize part flow.
- Support strategic investment decisions.

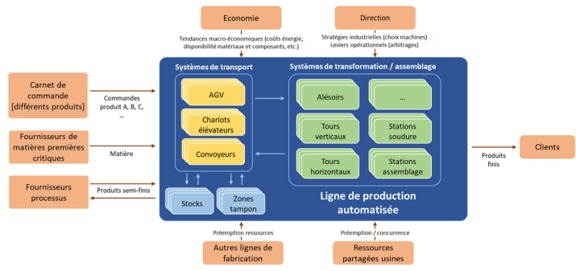
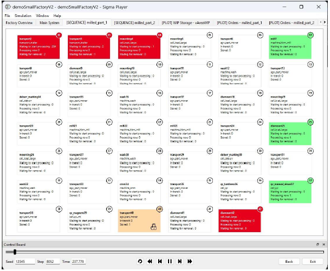
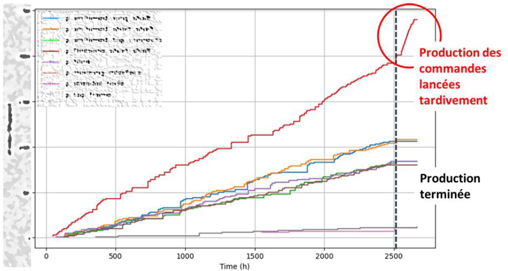
- Secured machine utilization and reduced part lead times (30% improvement against non optimized design).
- Improved flow stability and WIP control.
- Optimized sizing of lifting equipment and buffer zones.
- Enabled fast, iterative scenario testing.